
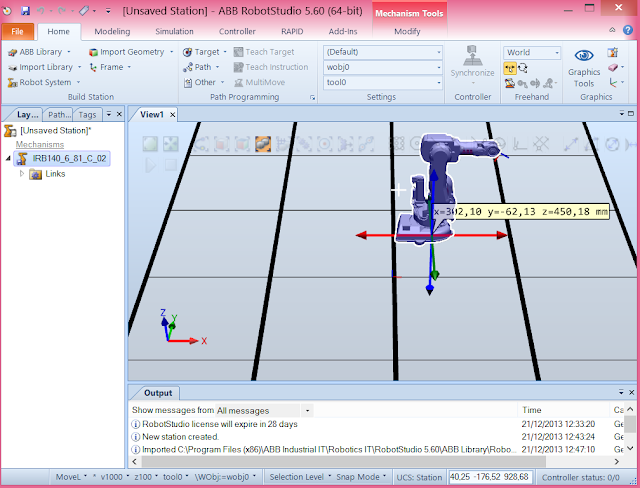
This changed radically in the late 1970s when several big Japanese conglomerates began producing similar industrial robots ( 6). For some time Unimation's only competitor was Cincinnati Milacron Inc. Unimation later licensed their technology to Kawasaki Heavy Industries and GKN, manufacturing Unimates in Japan and England, respectively. They were accurate to within 1/10 000 of an inch ( 5) (note: although accuracy is not an appropriate measure for robots, usually evaluated in terms of repeatability). They used hydraulic actuators and were programmed in joint coordinates i.e., the angles of the various joints were stored during a teaching phase and replayed in operation. Unimation robots were also called programmable transfer machines because their main use at first was to transfer objects from one point to another, less than a dozen feet or so apart. Engelberger in 1956, and was based on Devol's original patents. The first company to produce a robot was Unimation, founded by Devol and Joseph F. George Devol applied for the first robotics patents in 1954 (granted in 1961). Artificial intelligence, or what passes for it, is becoming an increasingly important factor in the modern industrial robot.
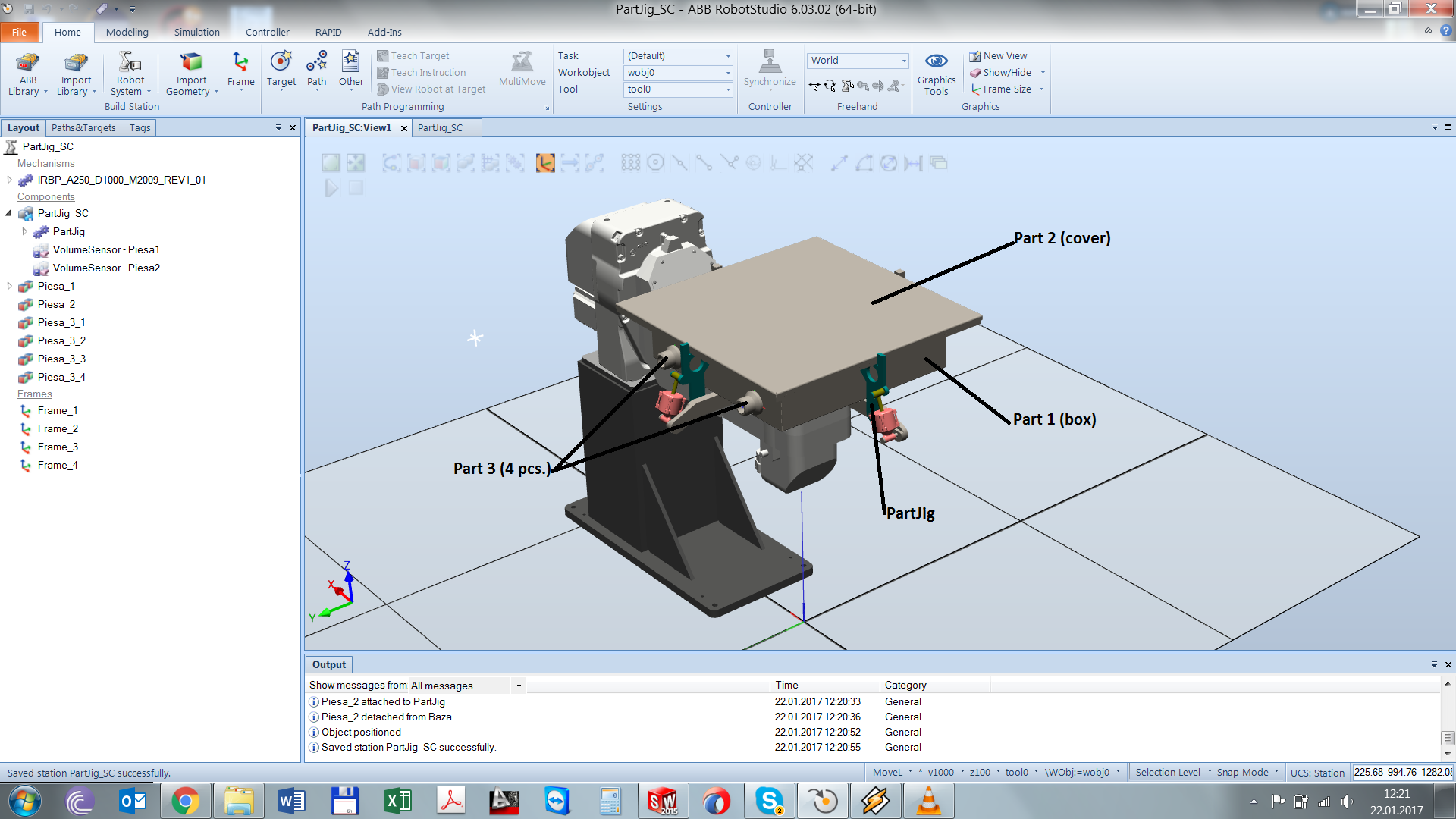
For example, for more precise guidance, robots often contain machine vision sub-systems acting as their ‘eyes,’ linked to powerful computers or controllers. Other robots are much more flexible as to the orientation of the object on which they are operating or even the task that has to be performed on the object itself, which the robot may even need to identify.

Abb robotstudio rotate grip series#
These actions are determined by programmed routines that specify the direction, acceleration, velocity, deceleration, and distance of a series of coordinated motions. Some robots are programmed to carry out specific actions over and over again (repetitive actions) without variation and with a high degree of accuracy. Robots exhibit varying degrees of autonomy:
Abb robotstudio rotate grip iso#
In the context of general robotics, most types of robots would fall into the category of robotic arms (inherent in the use of the word manipulator in the previously mentioned ISO standard). The most commonly used robot configurations are articulated robots, SCARA robots, Delta robots, and Cartesian coordinate robots (also known as gantry robots or x-y-z robots). Typical applications of robots include welding, painting, assembly, pick and place (such as packaging, palletizing, and surface mount technology), product inspection, and testing all accomplished with high endurance, speed, and precision. The most active industry in the application of robots is the automobile industry, and there is great interest in applying robots to weld and assembly operations, and to material handling. The demand for the use of robots stems from the potential for flexible, intelligent machines that can perform tasks in a repetitive manner at acceptable cost and quality levels.
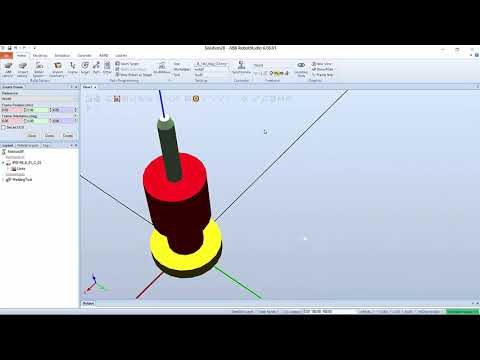
Industrial robots are essential components of today's factory, and even more of the factory of the future. The use of robots is also highly desirable in hazardous manufacturing operations such as spray painting, and welding that pose known health risks to human operators. Robots have been successful in automating simple and repetitive operations while simultaneously enhancing the quality of manufactured products in many production areas. In this context, robots have played an important role in the automation of various operations. In this respect, CIM can be viewed as a closed loop control system where a typical input is the order for a product and the corresponding output is the delivery of the finished product ( 5).Īutomation of the physical production processes on the shop floor is a key component of the CIM strategy for improving productivity. The CIM strategy is to integrate the information bases of the various units of automation within the conventional framework of manufacturing. To this effect, the concept of computer integrated manufacturing (CIM) has been introduced in various production environments with different purposes, including human productivity improvement, product quality improvement, capital resource productivity improvement, and provision of rapid response to market demands. In today’s global marketplace, manufacturing organizations are facing national as well as international competition, forcing them to further improve their performances. Khaksar, in Comprehensive Materials Processing, 2014 6.04.1.2 Industrial Automation
